There were many stalls
when I drove to work today.
But I got here fine.
I come to a light
the color of which is red.
The dashboard lights up.
Steering is GM.
Typically overboosted.
Time for alignment.
Ah, the lunchtime walk.
I went to check on the car.
Not leaking!... that much.
New driver's seatbelt.
Installed Saturday evening.
It works. I am pleased.
Monday, March 31, 2014
Friday, March 28, 2014
Takin' It To The Streets
Well, a second 3-day permit made it a legal Eagle and I picked it up from the shop Friday morning. I understand a little better what the shop meant about the rear brakes. They don't lock up, they just randomly apply and grind along for a while until they give up.
When I picked it up it ran... somehow worse than before. The engine idled very roughly and shook the car like it was about to fall to pieces. This was... disconcerting, since I had just paid for a diagnostic to look into just such driveability issues. At length I came to the conclusion that I should replace the spark plugs and see what that did for the idle. In the process of putting in 6 new plugs of my controversial preferred brand, I broke one of the ignition wires. That meant a new wireset had to go on too. With the new ignition components, idling felt significantly better, and the engine is slightly less apt to stall now. That, plus an 18" tailpipe extension, and I was ready for the Cone of Shame (the state emissions test).
The car got some confused looks in the service lane, and during the under-hood inspection I heard a "what's that?" at least once, referring to something in the engine.
Then the Cone of Shame went on the tailpipe, and Shame it was:
When I picked it up it ran... somehow worse than before. The engine idled very roughly and shook the car like it was about to fall to pieces. This was... disconcerting, since I had just paid for a diagnostic to look into just such driveability issues. At length I came to the conclusion that I should replace the spark plugs and see what that did for the idle. In the process of putting in 6 new plugs of my controversial preferred brand, I broke one of the ignition wires. That meant a new wireset had to go on too. With the new ignition components, idling felt significantly better, and the engine is slightly less apt to stall now. That, plus an 18" tailpipe extension, and I was ready for the Cone of Shame (the state emissions test).
The car got some confused looks in the service lane, and during the under-hood inspection I heard a "what's that?" at least once, referring to something in the engine.
Then the Cone of Shame went on the tailpipe, and Shame it was:
Of course, the Shame could be worse. You see that everything passes except hydrocarbons, which failed spectacularly. However, the guy I talked to there all but told me that this is probably due to old gasoline in the tank. It happens a lot with cars that have been sitting a long time. The gas gets old and doesn't want to burn, leaving unburned hydrocarbons in the exhaust. So as soon as I can get the right gubmint permit, I'll be running it around town, trying to burn off the old gas for a while, then trying the test again with fresh gas.
Thursday, March 27, 2014
The Cone of Shame
When we last left off, the Eagle was at a nearby shop, just to get
its carburetor tuned to increase the chance of it passing a state
emissions test, or "passing smog" as they say where I'm from.
Of course, you never know what's going to come to light when a fresh set of eyes starts looking at the internals of an old car. The phone call that came on Wednesday had some news that I did not expect. The guy told me that while they adjusted the carburetion, there were some bushings and gaskets on the thing that were problematic and most likely contributing to the stalling issue. Also, the rear brakes were, and I quote, "persnickety", in that they would sometimes lock up under relatively little braking pressure. Apart from that, the new exhaust pipe isn't sticking far enough out the back for the emissions test people to put the big cone thing* on it, that collects the exhaust gas.
There were a couple other little things that I'm not worried about right now, but what they recommended for the carburetor was total replacement with a re-manufactured unit, for the mere cost of upwards of $700. This is a reasonable price for professional work, but I could do the exact same thing myself for about $300, or if I'm feeling like a (frugal) glutton for punishment, I could pick up a rebuild kit for ~$20.
So the game plan for now is this: Forget about the carb and the brakes for the time being, and get a bolt-on exhaust tip that will stick out far enough to be able to test the emissions. If it passes, which seems possible, then I can register it. This buys me a ton of time to fix the brakes and carburetor at my leisure. If it doesn't pass, then I can get a 30-day permit, which buys me at least enough time to redo the carburetor, and I don't have to stress about using 3-day permits anymore, of which you can only use 3 in a year.
No pictures this time, 'cause, y'know, it's in the shop. Getting it back this afternoon though.
* "I do not like the cone of shame."
Of course, you never know what's going to come to light when a fresh set of eyes starts looking at the internals of an old car. The phone call that came on Wednesday had some news that I did not expect. The guy told me that while they adjusted the carburetion, there were some bushings and gaskets on the thing that were problematic and most likely contributing to the stalling issue. Also, the rear brakes were, and I quote, "persnickety", in that they would sometimes lock up under relatively little braking pressure. Apart from that, the new exhaust pipe isn't sticking far enough out the back for the emissions test people to put the big cone thing* on it, that collects the exhaust gas.
There were a couple other little things that I'm not worried about right now, but what they recommended for the carburetor was total replacement with a re-manufactured unit, for the mere cost of upwards of $700. This is a reasonable price for professional work, but I could do the exact same thing myself for about $300, or if I'm feeling like a (frugal) glutton for punishment, I could pick up a rebuild kit for ~$20.
So the game plan for now is this: Forget about the carb and the brakes for the time being, and get a bolt-on exhaust tip that will stick out far enough to be able to test the emissions. If it passes, which seems possible, then I can register it. This buys me a ton of time to fix the brakes and carburetor at my leisure. If it doesn't pass, then I can get a 30-day permit, which buys me at least enough time to redo the carburetor, and I don't have to stress about using 3-day permits anymore, of which you can only use 3 in a year.
No pictures this time, 'cause, y'know, it's in the shop. Getting it back this afternoon though.
* "I do not like the cone of shame."
Wednesday, March 26, 2014
The Once (and future?) Rally Champ
The road test that you see the beginning of in the last post went pretty well, considering. It stalled twice near the beginning but thereafter went about its business uneventfully. I'm sure the stalling has something to do with the engine not having been run very much in the last year, and that even when the carburetor was tuned, it was tuned for a much higher elevation (about 5000 feet, vs. about 1200 feet where I live). Also the high-octane gas is probably not helping either. But, the transmission shifted through all 3 forward gear ratios, which is exactly what I had hoped to get out of this first test.
The Eagle's at a shop right now, having the carb diagnosed and hopefully made happy. I picked the closest place to my house, but even that 2.5-minute trip was a white-knuckle ride. It was rush hour, and the car stalled twice, both times as I was stopped, waiting to turn. Even in neutral, I had to feather the throttle to keep it going. Once there, it took a while for the guy to understand that I don't expect an A+ emissions performance right away, just to be able to get to the test facility safely. Once that was made clear, things were a bit more relaxed and we got to talking about how cool a car it is, and how they used to rally these things back in the day, and so forth. So there's that.
In the meantime, enjoy some as-yet-unpublished photos of the fix-up process, up to now.
These next three were for reference, so that I could put things back together correctly.
The Eagle's at a shop right now, having the carb diagnosed and hopefully made happy. I picked the closest place to my house, but even that 2.5-minute trip was a white-knuckle ride. It was rush hour, and the car stalled twice, both times as I was stopped, waiting to turn. Even in neutral, I had to feather the throttle to keep it going. Once there, it took a while for the guy to understand that I don't expect an A+ emissions performance right away, just to be able to get to the test facility safely. Once that was made clear, things were a bit more relaxed and we got to talking about how cool a car it is, and how they used to rally these things back in the day, and so forth. So there's that.
In the meantime, enjoy some as-yet-unpublished photos of the fix-up process, up to now.
![]() |
the factory service manual in its usual spot on the fender |
![]() |
The transmission's underside, mostly reassembled after the rebuild |
![]() |
probably from draining the transmission before removal |
![]() |
a not-great image of the pile of mud I scraped off the starter motor |
![]() |
a view of the just-removed transmission |
![]() |
supporting the transmission after the transfer case was removed |
![]() |
mid-way through cleaning the transmission |
Monday, March 24, 2014
"I Got My New Shoes On And Suddenly Everything's Right"
As James May would say: GOOD NEWS!
It's not the Dacia Sandero, but it is the Eagle. And it's on its own feet again.
I put the rear drive shaft back in and tested it, and it worked perfectly. The exhaust is all the way in and clamped together, and (temporarily) hung with 16-gauge mechanic's wire. I serviced the rear differential and wired the transfer case selector (also temporarily) in 2WD. Stock-sized wheels and tires are on. It's been another busy weekend, and the Eagle now rests on the ground instead of jack stands.
Sunday night we had some dinner guests over, and right after they left, I nervously climbed into the driver's seat and fired up the engine. Then... well, here's a video for those who may not have seen it yet.
It's not the Dacia Sandero, but it is the Eagle. And it's on its own feet again.
I put the rear drive shaft back in and tested it, and it worked perfectly. The exhaust is all the way in and clamped together, and (temporarily) hung with 16-gauge mechanic's wire. I serviced the rear differential and wired the transfer case selector (also temporarily) in 2WD. Stock-sized wheels and tires are on. It's been another busy weekend, and the Eagle now rests on the ground instead of jack stands.
Sunday night we had some dinner guests over, and right after they left, I nervously climbed into the driver's seat and fired up the engine. Then... well, here's a video for those who may not have seen it yet.
Reinstall starter and bracePut in the transfer caseNew transmission fluid cooler line to replace the one I had to breakFix speedometerNew u-joints for the driveshaftsA new driver’s side CV axle in the frontInstall new exhaust components- Change oil and brake fluid
- Some new seat belts ($$)
New (stock) rims and tires ($$)- New shift indicator cable (which keeps the gearshift from moving accidentally)
- Service the front
and rear differentials - New gas springs for rear hatch
Insurance, operation permit, emissions, title, registration- Flush coolant and repair heater core with some stop-leak and a prayer
- Fix whatever makes the A/C compressor scream when it’s on
- De-grease the engine bay
- New under-hood insulation
- Interior detailing
- New paint job. Desperately needed. ($$$$)
Friday, March 21, 2014
Sad Panda
Alert readers will recall that I said there was a problem in the drive train last time. You may also remember that I mentioned that the new U-joints were almost as hard to install as the old ones were to remove. Well, either something happened during installation, or the bearing caps were just a little too big, or something else like that, but when the new joints were in place on the rear drive shaft, they could be moved back and forth only with difficulty, and one was almost impossible to move by hand, even though they came with the bearings pre-lubed, and I fully greased the joint before installation.
When the car is in gear, this causes a disconcerting creaking sound to vibrate through the whole shaft, and the stiffness makes it so that even with the car on jack stands, it won't go above 15 mph at idle without binding up and sort of bucking, in time with the rotation of the shaft.
Le sigh.
So the rear drive shaft had to come out again. For the first time in this project, I decided to seek professional help. I left early on Thursday with the drive shaft in my trunk to take it to a specialist shop on my way to work. When I put it on the counter, the lady told me I had put the U-joints in bass-ackwards, for one thing, (so much for trying to follow the picture on the box) but that wouldn't have caused the problem, and that I'd get a call a little later.
Even the shop was "not sure what happened" but they said nothing was bent, which was a relief. Even so, the U-joints needed to be replaced, and they recommended a balancing as well. Probably a good idea, since I doubt it's been done since the thing was manufactured. I picked it up after work Friday. Painted and everything, so that was cool.
Meanwhile, on Thursday afternoon I found out that the front drive shaft is rubbing on the front exhaust pipe. I'll probably just ditch that shaft for a while since I won't be using 4WD for the time being.
HOWEVER. I expect to be able to share some good news next time. Until then...
When the car is in gear, this causes a disconcerting creaking sound to vibrate through the whole shaft, and the stiffness makes it so that even with the car on jack stands, it won't go above 15 mph at idle without binding up and sort of bucking, in time with the rotation of the shaft.
Le sigh.
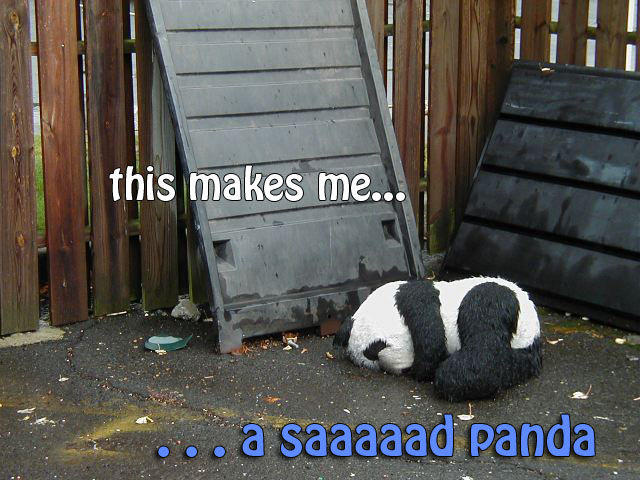
So the rear drive shaft had to come out again. For the first time in this project, I decided to seek professional help. I left early on Thursday with the drive shaft in my trunk to take it to a specialist shop on my way to work. When I put it on the counter, the lady told me I had put the U-joints in bass-ackwards, for one thing, (so much for trying to follow the picture on the box) but that wouldn't have caused the problem, and that I'd get a call a little later.
Even the shop was "not sure what happened" but they said nothing was bent, which was a relief. Even so, the U-joints needed to be replaced, and they recommended a balancing as well. Probably a good idea, since I doubt it's been done since the thing was manufactured. I picked it up after work Friday. Painted and everything, so that was cool.
Meanwhile, on Thursday afternoon I found out that the front drive shaft is rubbing on the front exhaust pipe. I'll probably just ditch that shaft for a while since I won't be using 4WD for the time being.
HOWEVER. I expect to be able to share some good news next time. Until then...
Wednesday, March 19, 2014
Right 'Round, Like a Record, Baby
Rapid progress sometimes comes at the expense of fatigue. That's pretty much where I am as I write this, on Saturday afternoon. Due to the infusion of cash from our tax refund, I've been able to get some of the last of the necessary parts for getting the Eagle on the road again. Add that to the fact that I got off of work early on Friday and that I'm eager to get most of this done before it gets hot, and you have many many hours of work, crammed into one weekend.
If you don't know, the area where I live has basically two seasons: Summer; and Summer's Comin'. Right now Summer's Comin' is winding down, and by the end of April it will be miserable weather to do major repairs in. So I worked at a fever pitch last Friday and Saturday. I finished putting the new CV halfshaft on at about 11 pm on Friday. Lots of WD-40 and PB Blaster were used, and no bolts were broken. Huzzah.
![]() |
once again, old vs. new |
Earlier that evening, I put in the new u-joints. They did go in a little easier than the old ones came out, but not by much. I also only smelled weed a little bit this time.
You'll note the grease fittings on the shafts and u-joints. I got to add "using a grease gun" to my automotive resume, right under "screwing up the nozzle of a grease gun" and "fixing the nozzle of a grease gun".
Saturday I hooked up both drive shafts. I tried to fix the speedometer but it doesn't seem to want to be fixed. I may have to have a shop look at it.
Next was the muffler. It fits with the tailpipe and intermediate pipe just fine. The intermediate pipe didn't want to fit in the cat, as previously mentioned, so I ground down the outside of it enough so that it could be forced in. Good enough. I stuck the muffler onto the back of that and supported it with jack stands.
Then, I could wait no longer.
It was... the big moment. The next test of the drivetrain. Could the transmission work under light load, and - *gasp* - turn the wheels??? Well, let's just say...

Also I managed to fix the speedo. Turns out the gear was in upside down. Rookie mistake.
But... there's another problem in the drive train. Which I'll talk about next time.
Reinstall starter and bracePut in the transfer caseNew transmission fluid cooler line to replace the one I had to breakFix speedometerNew u-joints for the driveshaftsA new driver’s side CV axle in the frontInstall new exhaust components (halfway done)- Change oil and brake fluid
- Some new seat belts ($$)
- New (stock) rims and tires ($$)
- New shift indicator cable (which keeps the gearshift from moving accidentally)
- Service the front and rear differentials
- New gas springs for rear hatch
- Insurance, emissions, title, registration
- Flush coolant and repair heater core with some stop-leak and a prayer
- Fix whatever makes the A/C compressor scream when it’s on
- De-grease the engine bay
- New under-hood insulation
- Interior detailing
- New paint job. Desperately needed. ($$$$)
Monday, March 17, 2014
Somebody Forgot to Say "No" to Drugs
On Thursday night it was time to
bust out some joints.
U-joints, obviously. You know, to
bust the old ones out of the drive shafts. I’m no pot-head. Although someone
nearby WAS smoking the ganja, and the smell of it was very strong out on the
back patio while I worked. So there’s that.
The universal joints were not in
good shape, although a couple might have had some life left in them. But in one
of them, the needle bearings had mostly been crunched into small pieces. In
another, there was no lubrication, since the hole under the cap, where the
grease comes through, had gotten blocked with a concretion of old, greasy dirt.
The online tutorial I read about
removing u-joints made it look pretty easy, and recommended that you use a
hammer and spark plug socket to bang the joints out. Like many of the Eagle’s
parts, they were pretty well stuck, and though I eventually managed to remove
all of them, my spark plug socket is a little the worse for wear:
![]() |
Those needle bearing-shaped grooves should probably not be there |
Let’s hope the new ones go in a
little easier after I clean the drive shafts.
Friday, March 14, 2014
"When I Was Younger, So Much Younger Than Today..."
Maybe some of the rest of you are like me. If you take on a project or task intending to do it yourself, it
practically kills you to have an unanticipated need to ask someone else to
help. It’s embarrassing, in a way. It kind of feels like, “hey, um, so I really
screwed up and bit off more than I could chew, and I need you to come bail me out. kthx.”
But it happens. So it was with
the Eagle’s transfer case. It was too heavy and oddly shaped to put in with my
merely human strength and inadequate tools. So on Tuesday I enlisted some help,
like I mentioned last time, and together we managed to finesse the case onto
the adapter housing and line it up just right to slide it into position.
The transmission ran great under
no load, and when I tested it with the transfer case attached, I got the same
results. One more hurdle cleared.
The one disconcerting bit that
keeps me from saying VICTORY again is that the speedometer doesn’t work. The
gear sits in the rear part of the transfer case and should have worked with
this test, so I’ll have to take that out and investigate.
Reinstall starter and bracePut in the transfer caseNew transmission fluid cooler line to replace the one I had to break- Fix speedometer
- New u-joints for the driveshafts
- A new driver’s side CV axle in the front
- Install new exhaust components
- Change oil and brake fluid
- Some new seat belts ($$)
- New (stock) rims and tires ($$)
- New shift indicator cable (which keeps the gearshift from moving accidentally)
- Service the front and rear differentials
- New gas springs for rear hatch
- Insurance, emissions, title, registration
- Flush coolant and repair heater core with some stop-leak and a prayer
- Fix whatever makes the A/C compressor scream when it’s on
- De-grease the engine bay
- New under-hood insulation
- Interior detailing
- New paint job. Desperately needed. ($$$$)
Tuesday, March 11, 2014
The Female of the Species
A slight change from the last
post. An alert reader on Oppo noted that the parts I had oh-so-cleverly found
for the transmission line connection aren’t even for cars at all, and probably
couldn’t hold the hose securely enough to be reliable. So it was back to the
drawing board, which in this case was the hardware section of Home Depot.
The associate I dealt with
quickly found a 3/8” barbed connector, but it was male, and I needed a female
connector. We searched the shelves, perplexed that there wouldn’t be female
version (“dad-gum female” were his words). But, a-ha, we located a 2-sided
female adapter, so we’re back in business.
The connections look like this
now, both at the radiator and the transmission. I added about a gallon of fluid
to test for leaks. None were immediately apparent, but I came back a few hours
later to find a small puddle and a slow drip. After a prolonged and silent “NOOOOOOOOOOOOOOO!!!!!!!!!1!1!”
and a realization that it was too dark to investigate further, I came back to
it after work the next day. The leak was probably from the torque converter
seal, which had had some time to dry out in the dry desert winter before I put
the fluid in, so I decided to tentatively move on.
I brought the battery in from the
back patio (longtime readers will remember the parts table back there), and
much to my relief, it still had more than enough electrons to turn over the
engine. I didn’t run it long enough to heat up the transmission fluid, just
enough to serve as a preliminary test. And also long enough to apparently
correct the leak from the front. I put in another gallon and checked the level with
the transmission in neutral and the engine running, and that topped off the
fluid level on the dipstick.
But now, now was the moment of
truth. Now that the transmission was full, I put it in gear. After a brief odd
sound, it seemed to be going all right. I looked under the car, and the output
shaft was spinning clockwise. VICTORY! I popped it back into neutral, and then
reverse. Looked underneath, and the output shaft spun counter-clockwise.
VICTORY AGAIN!
As a side note, this was all done
with half an exhaust system. The cat was hooked up, but nothing behind that,
and I’m not sure it was any louder than it was with the old system. So it seems
that the old muffler was doing what’s known as jack-squat.
Anyhow, victory was a little
short-lived. The transmission is still fine, but the next morning I attempted
to put in the transfer case. “Attempted” being the operative word. It was a
demoralizing, infuriating exercise in futility. The reason for this is that the
transfer case looks like this on the end that connects to the transmission:
It all has to line up to the
holes just right, and it’s basically impossible to line it up with a jack from
underneath, since the whole thing is so oddly-shaped. So I talked with a friend that night, the same friend of notable size and strength who tried to pull out the original torque converter in this entry, to maybe make the lift a team effort. The story of that, next time.
Tuesday, March 4, 2014
Keeping The Transmission Cool Under Pressure (400 PSI, that is)
The exhaust situation has hit a small snag. After I put in the new catalytic converter (pics below), I went to attach the
new intermediate pipe behind it. They’re made by two different manufacturers,
and just barely don’t fit together. I can probably get an adapter for that, so
it’s not a huge deal. Also, the muffler has been hard to find, but I think I’ve
found someone on eBay who has one, so hopefully that’s another crisis averted,
but the exhaust is at a standstill for the moment.
![]() |
The new cat, installed. You can see the transfer case sitting on a jack behind it. |
![]() |
Not hard to tell where the old pipe ends and the new begins |
It’s just as well, since I’m not
ready to start the car again just yet. The last link in that chain is ready to
go in place though. I’m referring of course to the transmission cooler lines. Earlier, I
had thought I would get new metal lines and connections, and custom bend them
to be like the old ones. Thing is, though, then I took the old lines out. All
the bends and curves and stuff were so convoluted that it was really hard to
pull them out of the narrow space they occupied. Custom bending new lines would
be hard enough, but getting them in without damaging them or anything else
would be impossible.
![]() | |
The old metal lines. |
So I settled on getting
high-pressure hoses instead. Turns out this was also easier said than done.
Transmission cooling hose, which - fun fact - can handle up to 400 PSI, is readily available, but not in the diameter I would
have needed to be able to clamp it onto the existing connectors. I’d have to
invent some way to adapt between the two. After a half-hour search of a local
parts store, with a very patient parts clerk and a not-so-patient 5 year-old son,
I found an arrangement that should work. Behold:
The teflon tape is necessary because the threads of the old connector are metric size, and the threads on the new one are a roughly (but not exactly) analogous SAE size, so it's not really tight without the tape. The new thing on the right + a new hose connected to the right side of it, replaces this:
![]() | |
The old connector + teflon tape + that new thing on the right. |
Subscribe to:
Posts (Atom)